Introduction
In recent years, most manufacturing companies have experienced external and internal unforeseen disruptions such as Covid-19, the Suez Canal blockage, the war in Ukraine, sudden market trends, machine breakdowns, and staff shortages. The disruptive events have taught us, that processes must be resilient to sudden changes.
Manufacturers must therefore make their processes more resilient to overcome unforeseen sudden changes. This article is the fourth step of the six-step “road map”, which is depicted in Figure 1.
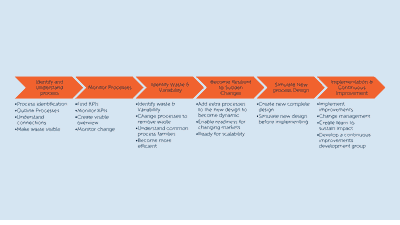
What is too lean?
In many years, the concept of lean manufacturing has become increasingly popular among manufacturers worldwide. The idea of eliminating waste and optimizing processes to achieve maximum efficiency and profitability has been on top of the agenda, and many companies have seen significant benefits from implementing lean practices when the business environment is predictable and unchanging. However, there is a danger in becoming too lean, as it can have negative consequences for a company's efficiency and profitability when deviations from a planned state occur unintended and/or unplanned[1]. When a company is too lean, it means that it is operating with minimal resources, minimising waste and maximising efficiency. While this approach can be effective in the short term, it can lead to long-term problems which can have a negative effect on cost, time and quality. For example, a company that is too lean may not have enough staff or equipment to handle sudden changes in demand, leading to delays and backlogs that can impact customer satisfaction and profitability.
Become resilient
First, what is resilience - There are many ways of explaining resilience in a manufacturing context. But in common all experts, professionals and academics agree that resilience usually is the ability to recover from an undesired state and to a desired state[2]. So, for a company to be resilient, it means that it has the capacity and ability to recover quickly from difficulties and disruptions. To achieve resilience, manufacturers must design a resilient system that makes their processes dynamic and able to overcome unforeseen changes. This can be achieved by first creating a robust system that secondly is agile.
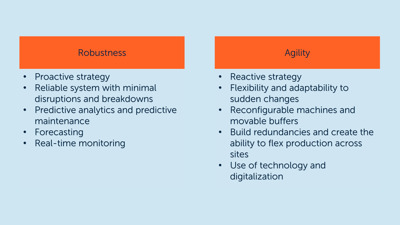
Robustness
Robustness refers to the ability of a system to maintain its functionality and performance even under unpredictable or challenging circumstances. Implementing a proactive strategy can help prevent unpredictability and disruptions. Creating a reliable production system with minimal disruptions and breakdowns is essential for achieving robustness. This can be achieved using various tools such as predictive analytics, forecasting, real-time monitoring, and predictive maintenance. By leveraging these tools, businesses can anticipate potential issues and proactively address them, thereby ensuring a more resilient and robust system ensuring long-term success.
Agility
Agility refers to the ability of a system to quickly and effectively respond to unexpected changes or disruptions. While robustness focuses on preventing and forecasting potential issues, agility implements a reactive strategy that enables a response to unexpected changes and disruptions, that are not handled by the robustness of processes. To achieve agility, there is a need for flexibility and adaptability to sudden changes. This can be achieved by designing a production system with reconfigurable machines and movable buffers[3]. Additionally, building redundancies and creating the ability to flex production across sites[4] is essential to enhancing agility. An agile production system can quickly respond to disruptions and maintain the continuity of operations, thus leading to a competitive advantage.
Case - Tesla's success in chip shortage
The Covid-19 pandemic has caused a significant disruption in the global economy, and the automotive industry has been no exception. One of the major challenges faced by the automotive industry during the pandemic was the shortage of semiconductor chips. According to Auto Forecast Solutions, almost 18 million vehicles will have been removed from production plans by the end of 2023 due to the chip shortage. Companies like Ford Motor Company have experienced losses running into billions of dollars due to a shortfall of 100,000 vehicles[5].
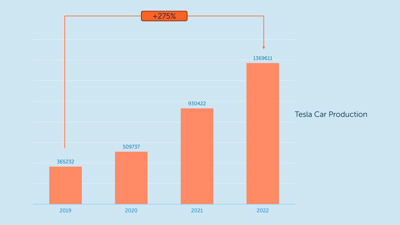
However, Tesla Inc. has emerged as an exception to this trend. While most other automakers struggled with production problems due to the chip shortage, Tesla managed to triple its car production from 2019 to 2022. Tesla's agility and flexibility enabled the company to adapt to the chip shortage quickly. When Tesla was unable to get the chips it had counted on, it took the available ones and rewrote the software that operated them to suit its needs. Tesla now sources about 1,600 different chips from 43 suppliers, which has helped the company maintain its production levels.
Actions / Tips & Tricks
- It’s important to think about the Resilience strategy
- Make sure to have a proactive and reactive strategy
- Instead of only relying on forecasts, begin to try out different worst-case scenarios
- Build a Lean system that still is flexible
- Rethink your process design by adding redundancies and buffers
Series of articles on process improvements
This is the seventh article in the series of ten.
- Potential Impact when Changing Processes
- Why Companies Should Focus on Optimizing Company Processes
- Roadmap on Redesigning a Company’s Processes to Enhance Competitiveness
Step 1 Identify and Understand your Processes
Step 2 Monitor your Processes
Step 3 Identifying Waste and Variability in your Processes
Step 4 Become Resilient to Sudden Changes
Step 5 Simulate your New Process Design
Step 6 Implementation and Continuous Improvement Process
The next article ‘Simulate your New Process Design’ describes why you need to do a simulation of the new process design and tools to do so.
[1] Reeves, M. and Whitaker, K. (2020). A Guide to Building a More Resilient Business. Harvard Business Review.
[2] Kusiak, A (2020). Resilient manufacturing. SpringerLink
[4] Risk, resilience, and rebalancing in global value chains | McKinsey
[5] Ford's pain underscores uneven impact of two-year au1. to chip shortage | Reuters