Introduction
Companies who focus on achieving best practice process design and -employee behaviour, and continuously improve their processes in a systematic way, have a great chance of achieving great overall process performance results and thereby become more competitive. However, many companies struggle to identify problems and optimization areas, or simply don’t know where to start, as problems quickly become complex. Therefore, many companies don’t enable or benefit from their full productivity and effectiveness potential.
PROCESS IMPROVEMENT IMPACTS
When companies optimize their processes and focus on continuous improvements and their people, the company enables the possibility of benefitting on multiple parameters such as financial impact, productivity impact and effectiveness impact. We usually experience that companies will reduce cost by more than 20% and improve lead-times and productivity with respectively more than 30% and 50% in specific areas of their operation.
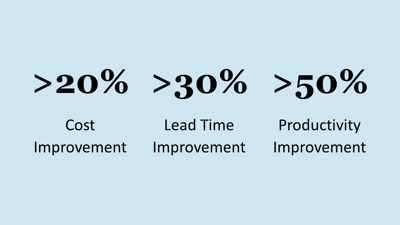
Such overall impact mentioned above can be obtained using a six-step roadmap seen in Figure 1, which is a structured way of optimizing processes to achieve best practice process design and perform continuous improvement.
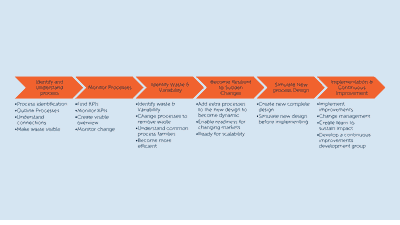
The first step of the roadmap focuses on process understanding, which is an essential base for optimization and is used as a baseline. Subsequently, a monitoring system must be established to effectively track the impact of process changes, e.g., reduction of lead time. Thirdly, variability, inefficiency, and wasteful activities in the processes should be identified to reveal optimization possibilities. Hereafter, the processes should be made robust and resilient to sudden changes, which of late has been proven to be neglected and thus more than ever of high importance. After this, basic and advanced simulation modelling can be applied to test different process designs and their potential impact on business performance, such as costs, lead times, and productivity. This enables management to make impactful and beneficial decisions on the implementation of process optimization to achieve best practice process design and continuous improvement. The roadmap is described more in-depth in the article ‘Roadmap on Redesigning a Company’s Processes to Enhance Competitiveness’ later.
Tips and tricks
- Identify and if possible, quantify your problem
- Create an overview of:
- Your main processes
- Machines/equipment
- Resources
- Create a mini business case
- What could be the potential improvements?
- Use cost-benefit analyses
- Remember to keep it easily understandable and not too technical if you have to sell the project/idea to a board/economics department
- Make a list of main stakeholders
Series of articles on process improvements
This article will be the first in a series of nine articles describing everything from potential impact, to why companies should optimize their processes and how companies should change their processes.
- Potential Impact when Changing Processes
- Why Companies Should Focus on Optimizing Company Processes
- Roadmap on Redesigning a Company’s Processes to Enhance Competitiveness
- Roadmap step 1: Identify and Understand Your Processes
- Roadmap step 2: Monitor your Processes
- Roadmap step 3: Identifying Waste and Variability in your Processes
- Roadmap step 4: Become Resilient to Sudden Changes
- Roadmap step 5: Simulate your New Process Design
- Roadmap step 6: Implementation and Continuous Improvement Process