Introduction
Many companies have generic processes, which have been functioning since their emergence. Therefore, managers and leaders often live by the motto “Why change something that works”. However, these seemingly well-functioning processes are often subject to inefficiency, low utilization, high variation, and wasteful handling, which results in hidden potentials and costs for companies. This article gives a brief description of the six-step “roadmap” seen in Figure 1 used to optimize companies’ processes and how they should be managed to enhance competitiveness. The roadmap has been based on real case studies and projects and is inspired by the steps of DMAIC, i.e., Define – Measure – Analyze – Improve – Control[1].
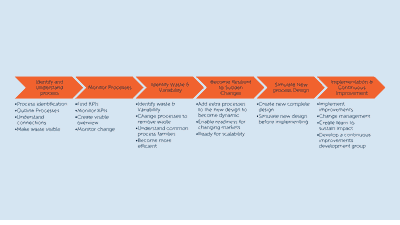
First step - Identify and understand proccesses
The first step in creating a sustained and optimized process design is to understand the company’s processes and human interaction/behavior. To do so, utilizing the Methodological Triangulation is beneficial, as it employs more than one method for data collection about one topic . This approach thus captures different dimensions of the same setup and system, while ensuring cross-validation of data collection. To obtain an accurate process flow, it is recommended to utilize the three data methods shown in Figure 2. Omitting one of these methods thus results in an inaccurate process flow mapping, which problematizes the implementation of changes and improvements.
Second step - Monitor processes
To monitor only the most relevant, it is important to establish a focus area of the optimization. The Pareto principle can be a very useful method to select the focus area. Hereafter, the relevant KPI’s within the focus area must be identified to define a baseline followed by a monitoring tool. The monitoring tool’s finest job is to visualize the improvements compared to that of the baseline, thus revealing trends. The tool can, furthermore, work as a foundation for daily, weekly, and monthly status meetings, proven to be an extremely important tool for managers and leaders wishing to monitor change.
Thrid Step - Identify waste and variability
After establishing the focus area, baseline and monitoring tool, the cause of the problem, i.e., waste and variability, such as unused human resources or redundant processes, must be identified. It is important when analyzing that the client is in focus, which means that all processes should be optimized to create the best customer experience. Additionally, after removing waste and minimizing variability, the new expected lead times and associated effects of the optimized flow must be calculated. This must then be examined and verified by management and key stakeholders to ensure that the newly created flow is optimal in practice for the company and not just theoretically. Lastly, a new process overview can be created to visualize the optimized flow.
Fourth Step - Become resilient to sudden changes
When a process design is completely striped down to perfection with minimal waste and variability, it can cause other concerns and risks within the robustness and resilience of the process design as companies today operate in a fast, turbulent, and ever-changing market. This environment challenges and forces companies to build a process design that focuses both on process robustness and agility to adapt to changes effectively . A process flow should therefore consider the possibilities for variances to enhance adaptability and readiness for scalability, which can be achieved by adding a buffer or creating a reconfigurable system in form of e.g., additional processes or machines. As illustrated in Figure 3, the additional process can support the critical process when required, thus ensuring resilience in the new process design and equipping companies for future changes.

Fifth Step - Simulate new process design
Simulation is a flexible, powerful, and intuitive tool imitating the operation or entire process flow, which is used to experiment with specific designs, and to estimate how well they will perform in different scenarios. Simulations can be conducted in various ways, from manually conducted to more automatic solutions. A company with limited resources and/or know-how, can with great success create simulations manually, without advanced systems, by trying out different variables for the new process design. A more automated solution is great if the resources and know-how are available, as it is extremely powerful and can run multiple scenarios (thousands) in a short time, thereby giving a statistical indication of how solid the new design is. Both the manual and automated simulation solution enables companies to see a possible effect on the process flow before the actual implementation, thus an excellent tool for testing and improving process performance before implementation.
Sixth Step - Implementation & Continous improvement
Lastly, employees of all levels must proactively work together to achieve incremental improvements to the optimized process design. Therefore, it is essential to change the behavior of the employees and incorporate a ‘continuous improvement’-mindset also commonly known as Kaizen. At first, it is crucial to prepare management to lead the change and provide them with tools to realize improvements. These tools can be Kaizen boards and daily meetings, which can be applied to celebrate small and quick wins. Another typical Kaizen tool is the Plan-Do-Check-Act, which is a more methodological approach for the control and continuous improvements of processes . Lastly, management must focus on employees’ resistance to change, where leaders beneficially can apply the Planned Approach to Change theory , where the focus is that change must happen at a group level rather than at an individual level.
Tips & Tricks
- When identifying processes, use workshops, observations, and data analysis to cross-validate the obtained data
- Understand the human interaction by incorporating resources and work tasks in the process flow map
- Before simulating the new design:
- Decide the constraints and variables of the process
- Setup a change team from the beginning
- Communicate to organization, stakeholders, or relevant employees to mitigate misunderstandings and resistance
Series of Articles on process improvements
This article is the third article in the series of nine:
- Potential Impact when Changing Processes
- Why Companies Should Focus on Optimizing Company Processes
- Roadmap on Redesigning a Company’s Processes to Enhance Competitiveness
Step 1 Identify and Understand your Processes
Step 2 Monitor your Processes
Step 3 Identifying Waste and Variability in your Processes
Step 4 Become Resilient to Sudden Changes
Step 5 Simulate your New Process Design
Step 6 Implementation and Continuous Improvement Process
[1] Dahlgaard, J.J. and Dahlgaard-Park, S.M. (2006). Lean production, six sigma quality, TQM and company culture. TQM Magazine, Vol. 18