Introduction
One of today’s manufacturing and service operations’ main challenges is increasing productivity, managing inventory, and optimising resource utilization. Over time, many different strategies, methods and concepts have been introduced and implemented in companies to overcome the challenges and to plan and control their operations. This article reveals the process of accurately assessing and mapping process flows by employing qualitative and quantitative identification methods to understand the processes. The article is the first step of the six-step “road map”, depicted in Figure 1.
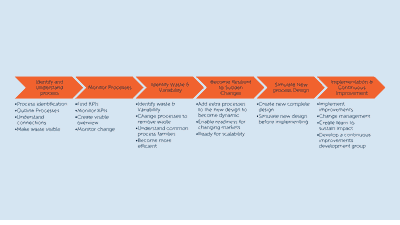
Identify and understand your processes
To create a sustained and optimized process design one must outline and map the process flow to visualize the current state situation. The process mapping will illustrate both inputs, activities, outputs, sequence, variances, and connections of the processes, which will benefit the company by providing a common understanding of the process flow. Furthermore, it helps the company to visualize details of the process, which is beneficial for decision-making when improving and redefining the processes and process flows.
However, the development of an accurate and realistic process flow has proven to be a difficult and unmanageable task for many companies. To achieve the most realistic and accurate process understanding, the methodical triangulation method shown in Figure 2 should be applied, which employs more than one method for data collection about one topic[1]. The method ensures cross-validation of data collection and captures different dimensions of the same setup and system, which is referred to as ‘Process Identification Triangulation Spot’. As depicted in Figure 2, to ensure cross-validation when creating an accurate process flow, it is recommended to utilize the following data methods: workshops, observations, and data analysis.
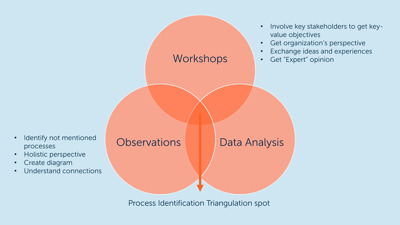
Omitting one of the methods results in a chance of an inexact process flow, which problematizes the implementation of changes and improvements. The three methods will be described more in-depth in the following sections.
Workshops
Workshops are a qualitative driven data gathering method and are important to gain the organization’s perspective, which is done by involving key stakeholders. Here, experiences, ideas, and inputs for process optimization can be shared and discussed, thus enabling the establishment of a common consensus for improvement. It is extremely important to involve key stakeholders as they have expert knowledge within the area. This involvement of stakeholders in the improvement process also results in stakeholders feeling heard and thus more likely to take ownership over improvements, which presumably makes stakeholders maintain the optimization. Utilizing this data method is essential, as, with poor guidance and competencies from stakeholders, the flow will have little attention to key-value objectives, which makes it difficult to improve the process[2].
Data Analysis
Data analysis is a quantitative driven method, which in this case is about collecting, transforming, cleaning, and modelling data, which is needed for confident and informed decision making in process optimization, as it provides a factually based insight to companies’ processes. In terms of process flow, data analysis can provide information about the sequence of processes, lead times, utilization, identification of waste, bottlenecks, and variation. If the company’s data is set up correctly, data collection and analysis is a powerful method, as it gives trustworthy insight to a business. Data thus allows companies to effectively determine the dominant cause of a problem and demonstrate why changes are needed. Methods applicable for modelling and understanding data are, among others, value stream mapping (VSM) and process mining.
Observations
Proceeding processes from a holistic perspective often requires lots of management time and systematic analysis approaches which tend to be time-consuming. Therefore, managers often set aside the importance of getting on the shop floor and observing the processes and instead tend to focus on daily tasks. However, observations provide qualitative valuable and necessary perspectives, used to identify unmentioned processes, waste, and inefficiency in processes. Moreover, observations are a great method to follow processes in real-time. Therefore, observations provide important information and insights into processes and daily operations.
The process identification triangulation spot
The quantitative and qualitative data gathering methods, i.e., workshops, data analysis, and observations should be applied to obtain the process identification triangulation spot (depicted in Figure 2), to create a sustained and optimized process design. Applying these data methods supports an accurate understanding of processes, which gives a strong decision-making tool for further analysis and decisions on process optimizations and is the first step required to make continuous improvements.
Actions/ Tips & Tricks / Dos & Don'ts
- Make sure to select the right stakeholders
- Pay attention to variances when collecting data
- Try to identify where there can be waste in your processes
- Start empowering ownership within your stakeholders to prepare for change
Series of articles on process improvements
This is the fourth article in the series of nine.
- Potential Impact when Changing Processes
- Why Companies Should Focus on Optimizing Company Processes
- Roadmap on Redesigning a Company’s Processes to Enhance Competitiveness
Step 1 Identify and Understand your Processes
Step 2 Monitor your Processes
Step 3 Identifying Waste and Variability in your Processes
Step 4 Become Resilient to Sudden Changes
Step 5 Simulate your New Process Design
Step 6 Implementation and Continuous Improvement Process
The next article ‘Monitor your Processes’ gives an insight in some methods that can be used to monitor the processes and thereby create a baseline.
[1] Denzin, N. (2006). Sociological Methods: A Sourcebook. Aldine Transaction. (5th edition).
[2] Johansson, A. and Nafisi, M. (2020). Process mapping in industry – the self-centred phenomenon and how it affects continuous improvements. Elsevier B.V.